However, maintenance costs for all-composite products are significantly lower if any during their long service life.
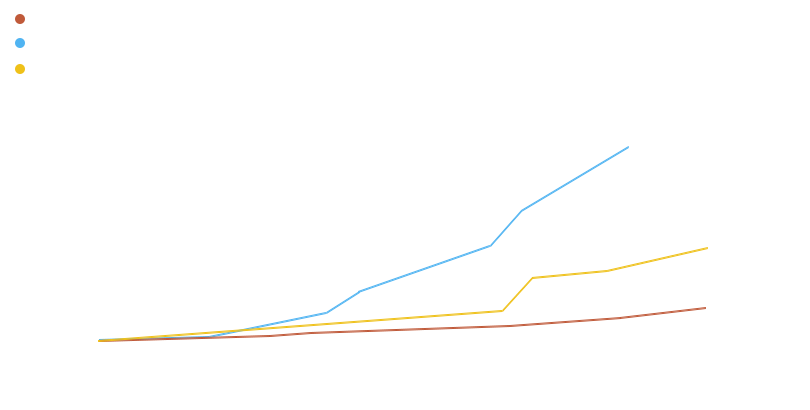
However, when it comes to a single structure, combination of composite material with metal elements (so called hybrid structures) does not solve the issue with corrosion as long as the overlap with inert materials result electrochemical corrosion.
It’s important to note that application of metal elements assumes drilling holes. The anisotropic properties of pultruded composite profiles exclude this practice since it lead to the loss in bearing capacity and higher fragility of the structure.
To summarize the above stated, switch to constructions of composite materials is appropriate only when there are technical solutions allowing to eliminate metal elements and create all-composite structure.
The design of our constructions insures convenient replacement of their elements in case of an accident or repair.
Material Density (Т/м3) Steel 7,7-7,9 Aluminum 2,7 Composite 1,7 — 2
Lightweight of composite structures has great practical importance.
Application all-composite constructions greatly reduces load on supporting structures. For comparison: the weight of one lineal meter of metallic handrail fence can be up to 80 kg on each side of the bridge structure, while the weight of lineal meter of all-composite handrail fence is 20 kg. It means that for every 10 m handrail fence the difference is 1200 kg. Reducing the weight of artificial structures allows for better use of load-bearing capacity of the structure, as well as to extend its operating life.
Easy process of installation reduces labor costs (2 workers are enough) and saves from expenses for special technique.
According to scientific research electrical resistance of glass fiber equals to ρ = 109 – 1012 Ohm * m, that is literally tens of thousands times higher than of any metal. These properties are maintained stable under the most severe conditions.
Low shielding efficiency makes this material ideal for usage next to radio stations or other equipment when keeping same frequency of radio wave reception is essential.
Opposite to metal, polymer composite materials do not impose any threat as an antenna for different radio frequencies that can interfere with electronics located in the roadway e.g. in road surveillance cameras.
Composite materials based on fiberglass and unsaturated polyester resins have a very low coefficient of thermal expansion. This allows you to use such material for areas with large daily and seasonal temperature changes. It allows to use this material in the areas with large daily and seasonal temperature changes.
The results of testing confirms that at a temperature variation from 23ºC to 40ºC, the coefficient of thermal expansion of composite material is 53.30 μm / m · ℃.
Currently available data on the natural aging of FRP composites proves that long exposure (over 10 years) in the natural environments has almost no effect on its strength characteristics (98% of the initial parameters).
Testing results
The durability of composite products is determined by the influence of specific as well as complex climatic and service factors.
Preservation of properties by polymer composites under long-term climatic effect can be accessed by the results of their artificial aging. It simulates the effect of various climatic factors: long-term exposure to high temperature, daily, seasonal and annual temperature fluctuations, solar radiation and others. The nature of variation of mechanical properties of composite in the process of accelerated heat aging confirms the fact that their properties remain stable under exposure to high heat during 50 years.
Under the influence of natural aging and water, properties of the polymeric binder are changed in relation to water absorption. While the production based on pultrusion process minimizes the water absorption index down to 0.5%. In its turn it increases the period of mechanical properties change for more than 50 years.
Properties of the polymeric binder by water vary depending on the coefficient of water absorption of the material. Manufacturing of composite products based on modern pultrusion technology minimizes water absorption index, bringing it to 0.5%, which increases the period of change in mechanical properties of the material in a moist environment.
This method solves the problem with paint cracking or flaking, because pigment is sealed into the structure of the material. UV protection protects the pigment from fading.
Upon delivery FRP handrail fence our company also supplies accessories for installation: composite anchor and two-component adhesive for chemical anchoring.
Composite anchor has some significant advantages comparing with anchors made from traditional material and gives us the great opportunity to completely avoid an application of anchor made from traditional material. It is allowing to call our products -all-composite constructions. This fact allows to increase the lifetime of fastening elements as well as handrail fence constructions and thereby prolongs their life cycle and decreases the costs in usage period.